Seis Sigma se define como un método de gestión de calidad combinado con herramientas estadísticas; cuyo propósito es mejorar el nivel de desempeño de un proceso mediante decisiones acertadas, logrando de esta manera que la organización comprenda las necesidades de sus clientes.
El Seis Sigma se apoya en el sistema de mejora llamado DMAIC, el cual sigue las siguientes 6 etapas:
- Definir el proyecto, se en enfoca en delimitarlo. Al finalizar la etapa, se debe tener claro el objetivo del proyecto, la forma de medir su éxito, alcance, beneficios y el personal que interviene en este.
- Medir, su objetivo es entender y cuantificar la magnitud del problema o situación que se aborda con el proyecto. El proceso bajo estudio se define a un nivel más detallado para entender el flujo del trabajo; los puntos de decisión y los detalles de su funcionamiento y sus métricas se establecen detalladamente.
- Analizar, las variables de proceso definidas en la etapa de medir deben ser analizadas mediante técnicas estadísticas para observar su contribución a la variación del proceso.
- Mejorar, se proponen e implementan soluciones que atienden las causas raíz para asegurar que se corrijan o reduzcan los problemas identificados. La clave para generar mejoras es elegir soluciones que ataquen la fuente del problema y no el efecto.
- Controlar. Consiste en diseñar un sistema que mantenga las mejoras deseadas una vez que han sido alcanzadas.
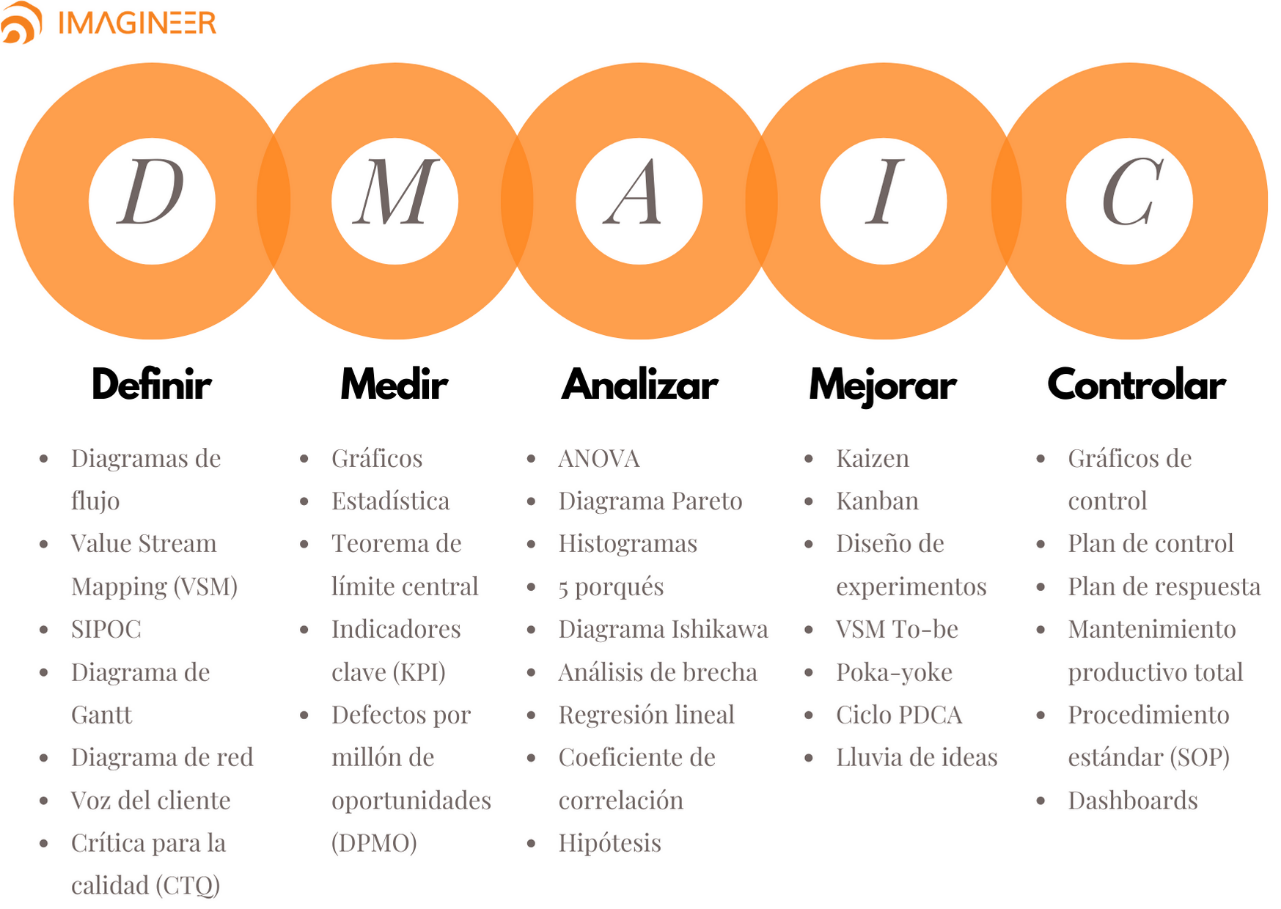
Caso a desarrollar
La aplicación se efectúa en el área de almacén de una empresa, que tuvo como objetivo reducir la variabilidad de los procesos de la Cadena de Suministro para incrementar el nivel de servicio, mejorando con ello el desempeño de la Cadena de Suministro. Este se realizó en las siguientes etapas.
Etapa 1: DEFINIR.
Se identificaron áreas de oportunidad significativas en cada una de las etapas de la cadena. de suministros. Un área de oportunidad que se encontró en el almacén fueron en las actividades de recepción, almacenamiento y la consolidación de mercancía para su distribución, además se realizó un diagrama de Pareto para determinar los factores con mayor incidencia.
En la figura se puede observar, que la principal área de oportunidad es el producto sin recepción del almacén de productos terminados, en donde la empresa recibía contenedores que eran transportados en camiones desde los diferentes puntos de la empresa para su distribución a tiendas.
Un vez identificada el área de la oportunidad se desarrolló un mapeo de procesos (llamado también SIPOC (por las siglas en inglés de Supplier, Input, Process, Output y Customer), con la finalidad de observar y entender cómo se realizaban las actividades del almacén en general y de la recepción del producto.
Se obtuvo que el tiempo de descarga, la organización de lotes de entrega y la carga por pedido de los clientes era excesivo y ocasionaba una permanencia demasiado larga de los productos terminados en almacén que, en ocasiones, saturaba su capacidad haciendo necesario que se rentaran bodegas externas a la empresa para resguardarlos.
Adicionalmente, una débil organización de las actividades de recepción y descarga ocasionaba errores y demoras en las entregas a los distribuidores, y un gasto excesivo de horas extra de trabajo daba la pauta para trabajar con esta variable.
La dirección, en conjunto con los proveedores, estableció seis puntos esenciales para cumplir con la satisfacción del servicio de recepción del almacén.
Entre los criterios de evaluación se encontraban: el tiempo de recepción, el desempeño en la recepción, el tiempo de liberación de la unidad, el conocimiento del área, la reacción de la organización a las quejas del cliente y la satisfacción general.
A las variables críticas para calidad del servicio prestado por el almacén, se les determinó y clasificó el nivel importancia. En una matriz elaborada para evaluar este proceso con los proveedores y de negocio se muestran las calificaciones bajas asignadas por los Proveedores 1 y 2 que indicaron la necesidad de acciones de mejora.
Etapa 2: MEDIR
Una vez determinadas las variables a trabajar para reducir la variabilidad del producto sin recepción de los Proveedores 1 y 2; se procedió a la medición de tiempos de entrada y de descarga de las unidades que contienen el producto terminado.
La dirección marcó como tiempo de estudio meta para las entradas de unidades: 60 min +/- 10 min. La presentación de datos se realizó por medio de gráficos de valores individuales representado un punto real de cada observación en un grupo ya que con éste resulta fácil determinar los valores atípicos y la dispersión de la distribución. Esto corresponde cuando el tamaño de la muestra menor a 50 datos, como en este caso.
Se utilizó un análisis seis en uno, por su presentación de datos completos y gráficos para una fácil interpretación de los mismos. El análisis mostró que los datos se comportaban normalmente con una variación en los tiempos de entrada σ = 24.77, indicando que el proceso era inhábil para cumplir con los requerimientos de nuestros proveedores por la Capacidad del proceso Cp = 0.47.
El Cp es el índice que se usa para evaluar el proceso y este índice separa y evalúa la variación y centrado. Por la finalidad del estudio interesa conocer la variación del proceso y no tanto la ubicación. Se observa que tiene un PPM = 161,791.68 (partes por millón de defectos) mostrando que el proceso está arrojando mucho defectos y las entradas de las unidades están fuera de control.
El segundo análisis de la variable es la descarga, con un tiempo establecido por la Dirección de 60 min + 10 min.
En la figura se muestran los datos del segundo análisis, los cuales se comportan normalmente, con una variación en los tiempos de descarga σ =37.33, indicando que el proceso es inhábil para cumplir con los requerimientos de los clientes por el Cp = 0.31. Su PPM = 406,882.24 (partes por millón de defectos) muestra que está descontrolado el tiempo de descarga de las unidades.
Etapa 3: ANALIZAR
El proceso arroja mucho defectos, por lo que se realiza un análisis de causa y efecto para determinar cuáles son las posibles causas-raíz de los efectos presentados:
El diagrama de causa y efecto muestra las posibles causas raíz del área de oportunidad (producto sin recepción), proporcionando información necesaria para plantear las hipótesis sobre los tiempos de descarga de los operarios y sobre los métodos de acomodo del producto.
Primera hipótesis: Los cuatro operarios tienen el mismo tiempo de descarga
El P-valor indica el criterio de aceptación y rechazo: H0 se rechaza si la significancia observada es menor que la significancia predefinida, o sea, si p-valor< α , en caso contrario si el p-valor> α, no se rechaza H0. Por lo anterior se acepta la H0.
El R2 del modelo anterior se acerca a 0. Se examina la gráfica de residuos para determinar los supuestos de normalidad.
Los residuales se ubican a lo largo de la línea ajustada que se encuentra entre los bordes de confianza, sólo un valor atípico se encuentra alejado de línea de normalidad. Los supuestos del p-valor es mayor que 0.05 y la µ tiende a 0, por lo que es posible establecer que los residuos siguen una distribución normal, proporcionando evidencia para que el modelo anterior se considerará para el análisis de la variable.
Se verificó el supuesto de que los residuos están distribuidos aleatoriamente y tienen una varianza constante del modelo unifactorial.
Conclusión de la prueba de hipótesis: El análisis estadístico de la figura muestra el valor de p es menor a 0.05. Se concluye que al menos uno de los operadores afecta más en el tipo de la descarga que el resto de sus compañeros. Esto comprueba que la variación entre los niveles de operadores es una variable significativa que afecta a la variable Y (tiempo de descarga).
Segunda hipótesis: Los métodos de acomodo del producto influye en el tiempo de la recepción.
Conclusión de la prueba de hipótesis: El análisis estadístico muestra en la figura, que el valor de p es menor a 0.05. Se concluye, que si hay una diferencia estadísticamente significativa entre los dos métodos. Por lo que, si es posible afirmar que un método alarga más el tiempo de recepción que el otro. Por lo que, el método si es una variable significativa que afecta a la variable Y (tiempo de descarga).
Etapa 4: MEJORAR
Después del análisis de la hipótesis, se procede a buscar la solución con un Análisis de los 5 Por Qué’s, que es una técnica sistemática de preguntas utilizada para el análisis de problemas y para buscar las posibles causas y soluciones. Consiste en preguntar por qué cinco veces, por cada problema encontrado con el objetivo de ir más allá de los síntomas evidentes, hasta que la verdadera causa del problema se torne clara y se encuentre la solución más efectiva. En la figura, se muestra un análisis realizado.
Como solución al área de oportunidad (producto sin recepción), se comenzó con la estandarización de los procesos y la capacitación al personal del área desarrollando las ayudas necesarias para la disminución del esfuerzo realizando las operaciones más ergonómicas. Además, se desarrolló un formato donde se registraron las frecuencias de las unidades que realizan las áreas involucradas.
Etapa 5: CONTROLAR
El control se llevó al cabo mediante una hoja de chequeo de entrada, descarga y salida de las unidades del almacén. Estos datos fueron registrados con el objetivo de valorar la variación de las frecuencias de entrega. Así, las áreas tuvieron una forma tangible de medir los procesos y tomar medidas preventivas o correctivas; para cumplir con los objetivos planteados.
RESULTADOS Y DISCUSIÓN:
Concluida la aplicación de Seis Sigma en el almacén de producto terminado de la industria textil, se evaluó el logro de la finalidad de la metodología de reducir la variabilidad de los procesos analizados. A continuación, se muestra los estadísticos de frecuencia de las variables fuera de control que se estudiaron previamente en la tabla:
La figura muestra los resultados del segundo análisis de capacidad de proceso del tiempo de entrada, el cual presenta normalidad con una variabilidad σ = 3.448, mostrando un proceso hábil que cumple con los requerimientos del cliente con un Cp = 1.93, y con un mínimo de defectos por millón en el proceso PPM = 1.87.
Con las alternativas aplicadas a la segunda variable, se obtuvo el tiempo en minutos de descarga de unidades después de una mejora; estos resultados son presentados en la siguiente tabla:
Tiempo en minutos, descarga de unidades después de mejoras
La siguiente figura muestra los resultados de análisis de capacidad de proceso de descarga de unidades, el cual muestra normalidad con poca variabilidad (σ = 3.251). En los datos se observa un proceso hábil que cumple con los requerimientos del cliente y un Cp = 1.79, con un mínimo de defectos por millón en el proceso PPM = 2,546.36.
La siguiente tabla muestra los resultados de la aplicación de la metodología en el almacén, mostrando los datos anteriores y posteriores de la misma.
Los almacenes son medidos por su OEE (Eficiencia Global del Equipo), tomando como referencia tanto al equipo como el conjunto de personas para y estableciendo como realmente se están utilizando los recursos permaneciendo por debajo de la meta establecida de la organización. OEE = razón de disponibilidad x razón de rendimiento x razón de calidad. La siguiente tabla se presenta un resumen de los problemas que se tenían a causa de la variabilidad de estas dos áreas por unidad.
Además, se presentó un decremento en métricos representativos como el tiempo extra generado por parte del área en un promedio de 10 horas por semana y otros gastos como alimentos y gasolina. La siguiente tabla refleja la reducción del 40% en el tiempo extra de las horas utilizadas para el transporte de las unidades por atrasos. El 60% restante es el proceso en cambios por producción.
Antes de la implementación de la metodología Seis Sigma, no se trabajaba en base al tiempo-ciclo de descarga, por lo que fue preciso efectuar una medición que fue de un tiempo de descarga de una unidad de 118.4 minutos. Al reducirlo al objetivo de un tiempo descarga por unidad de 20.63 min, se logró un porcentaje de reducción del 82.57%.
Conclusiones
La interacción y la variabilidad de la Cadena de Suministro, es un problema importante de las empresas presente en el actual entorno demandante. La ventaja de la metodología propuesta consiste en la utilización de herramientas para áreas administrativas y productivas en la superación de los problemas de la variabilidad entre los procesos de la Cadena de Suministro de las organizaciones.
La metodología Seis Sigma, puede ser aplicada a cualquier organización con una Cadena de Suministro establecida con variantes en la utilización de las herramientas para analizar los resultados que pueden ser sencillas o complejas en función del problema y su contexto. Este enfoque de herramientas básicas de apoyo a la Cadena de Suministro permitió reducir la variabilidad en el almacén de producto terminado. Con ello, este análisis proporciona evidencia para afirmar el resultado exitoso del uso de Seis Sigma para la solución de problemas en la empresa y la reducción de la variabilidad, atribuida a los diferentes elementos de la Cadena de Suministro.
Este estupendo estudio fue hecho por:
Martinez José, Garcia Ernesto y Estela Carmen
Revisar el journal: Aquí